1.Equipment Manufacture
Chaeng takes sole responsibility of all problems of grinding plant construction in EPC. Chaeng could select some main equipment basing on rich experience, so the
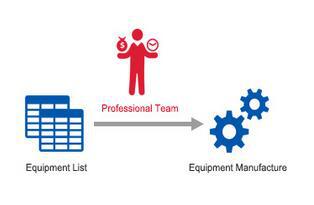
mine design is in step with equipment manufacture, which greatly shortens the construction period, and saves time and cost for customers. In order to strictly control the period, Chaeng will formulate detailed and feasible project schedule in EPC, and project control group strictly supervise the progress of project.
2.Installation & Commissioning
1)Installation & commission technology
Installation & commission is key link of raw material test, mine design, and equipment manufacture, and directly takes influence on production.
Installation and commission of grinding plant equipment is a very careful work with strong practicality. Any error may lead to low capacity which cannot reach the expectation. For example: in different construction, the same type of equipment would have deviation because of the opening location and installation etc. These differences will have a significant impact on the final production efficiency.
In view of the importance of installation and commission, Chaeng established professional installation company having four installation teams which are from the mine
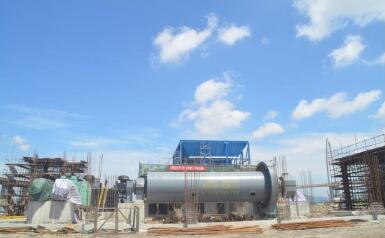
production line and led by engineering technicians who held the directors of grinding plant and mine leader. Installation personals Chaeng sent out participate in the whole mine design of clients, and there are two points for this: one is the old technicians are very familiar with structure, performance and using of Chaeng equipment; the other is the technician who can quickly solve many actual problems in plant construction understand the overall design of factory because of participating in the whole mine design.
2)Methods of Installation and Commission
For installation and commission, Chaeng upholds customer fist. There are 3 methods of installation and commission according to the actual situation of customers.
①Free guide of installation
Chaeng can send related technician to guide customer with the equipment installation and commissioning for saving customer's cost.The customer should responsible for the travel charge of the technician.
②Contract for materials
Chaeng arranges the installation and commission technicians, and clients prepare the components and instruments of installation of commission.
③Contract for labor and materials
Chaeng is responsible for tools, materials and personnel allocation of the installation and commission. Customers can directly wait for the final results.
3.Personnel Training
It is simultaneous for worker training and installation & commission in order to save time and cost. Worker training has two purposes, one is the grinding plant works earlier and produces benefit; the other is training technical team for customers to guarantee the normal operation of the factory in the future.
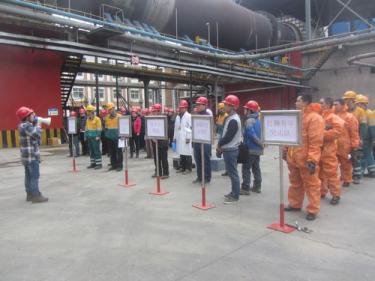
The technicians who have extremely rich practical experience for worker training are experts of installation and commission team. They help workers to pay attention to some details which usually don't be easy to notice but extremely important. These Chaeng technicians provide training from 3 aspects:
1.Operation training for all workers involved in mine grinding processing
2.Training for the common problems in the plant operation and processing technology; a live solution demonstration for workers
3.Training of operation experience grasping, the workers should operate machines by lots of exercises.
Through the above three aspects of training, workers could skillfully operate mine grinding technology (grinding particle size, adding burdening etc.) and processing equipment. Customers have their own technical team, which can prevent the dressing plant from long time stop.
When the training is completed, Chaeng Company will present free “Common faults handling of mining equipment”, “The operating procedures of processing plant” and common forms, which is convenient to manage operation of grinding plant.